Improve Quality and Reduce Costs
Adhesives play a critical role in improving manufacturing processes, construction, and various industries by enhancing product quality while simultaneously reducing costs. Here’s how:
1. Improved Quality
Stronger and Uniform Bonds
Adhesives provide consistent bonding across surfaces, ensuring a stronger, more uniform hold compared to traditional fastening methods like screws or nails. This reduces weak points in the structure.Material Versatility
They can bond a wide variety of materials, such as metal, wood, glass, plastics, and composites, enabling innovative designs and combinations that would otherwise be difficult or impossible to achieve.Enhanced Durability
Adhesives create seals that are resistant to moisture, temperature fluctuations, and vibrations, extending the life of products and improving overall reliability.Lightweight Solutions
By eliminating the need for bulky fasteners, adhesives contribute to lighter, more efficient designs, especially important in industries like automotive and aerospace.Aesthetic Advantages
Adhesives provide a seamless finish with no visible fasteners or weld marks, leading to cleaner and more professional-looking products.
2. Cost Reduction
Lower Material Costs
Adhesives reduce the need for additional materials like screws, bolts, or rivets, cutting down on production costs.Faster Production
Many adhesives are quick to apply and cure, speeding up assembly processes and reducing labor time. Automation of adhesive application further optimizes efficiency.Reduced Equipment Costs
Adhesive use minimizes the need for expensive machinery, such as drilling tools or welding equipment, saving capital and maintenance costs.Fewer Repairs and Replacements
High-performance adhesives prevent problems like leaks, cracks, and corrosion, reducing maintenance and repair costs over time.Lower Transportation Costs
By enabling lightweight designs, adhesives reduce the overall weight of finished products, leading to lower shipping and fuel costs.
Adhesive Manufacturer helps reduce total costs
Adhesive Manufacturer, Supex, Ensures lowest total adhesive cost.
Does user require lowest cost of adhesive OR lowest application cost.
Total Application cost = Cost of adhesive used per application + Labour cost in applying the adhesive + savings due to lesser warranty claims, failure costs.
Supex, an adhesive manufacturer , ensures to keep the TCO lowest. We will discuss in details about this concept and how we ensure lowest TOTAL COST.
The total cost of ownership (TCO) is a management accounting concept that derives an asset’s total cost during its useful life. It includes the purchase price, maintenance and operational cost that will incur during the asset’s lifespan.
- Total cost of ownership (TCO) refers to the lifetime cost of buying an adhesive/sealant. In simple terms, we can say that it is the total monetary cost attributed to an asset spanning from the purchase planning to its disposal.
- TCO analysis helps to disclose all direct, indirect as well as any hidden costs associated with a purchase. Therefore, it’s helpful to examine whether a cost-effective product is as economical as you think.
- The formula to calculate the TCO is to add the initial purchase value to direct, indirect and other hidden costs. The value so arrived is then subtracted from a projected resale/ residual value at the end of the asset’s lifespan.
- These costs may change depending on what you’re buying and what’s your purpose of the purchase. Also, hidden cost varies with the asset type.
HOW IS TOTAL COST OF OWNERSHIP CALCULATED?
The next time you are selecting new equipment, try using the total cost of ownership (TCO) formula:
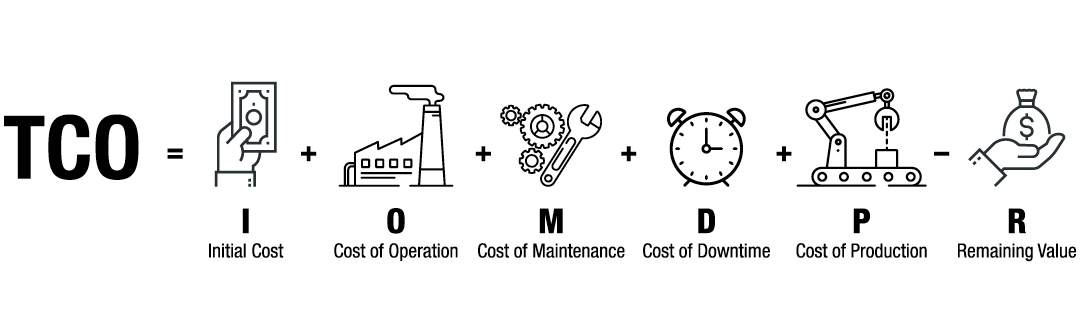
I = INITIAL COST
The initial cost is the number that appears on the price tag. As previously stated, this is less than 10 percent of the Total Cost of Ownership (TCO).
O = OPERATION
Operation is the cost to install the pump, test the pump, train employees to run the pump, and the cost of energy to operate the pump. If the pump is complicated to use, the cost of training will increase.
M = MAINTENANCE
Maintenance includes the cost of regular repairs such as cleaning, inspecting, lubricating, and adjusting the pump to make sure it is in optimal condition. This also includes reactive maintenance when the equipment breaks down unexpectedly.
D = DOWNTIME
While you could include downtime along with the cost of maintenance, it is often so large that it warrants its own category. Downtime involves the labor costs of employees whose work is delayed, indirect labor costs from supervisors who address the issue, lost production, and lost customers from inability to meet time expectations.
P = PRODUCTION
Two different pumps will likely have different levels of output, produce different qualities, and have different environmental implications.
R = REMAINING VALUE
The remaining value has to do with the pump’s longevity. How much will the pump be worth in 5 or 10 years? It can be a big difference.
This formula can sound a little overwhelming, but let’s start simple.
I + M – R = TCO
Case Study – Lowest total application cost
APPLICATION: TIE ROD HOLE SEALING
Costing of Cement Grouting method
Considering the length of the hole to be 500 mm, with a diameter of up to 50 mm
- 1 bag of 25 kgs (can fill up to 75 holes) = INR 450/-, material cost = Rs 6 per hole
Labor cost: 2 labourers will grout 50 holes per day. Let us assume they are paid INR 750/- each. Labour cost per hole= Rs. 30.
- Cement grouting cost per tie rod hole= Rs 36
This process is tedious, labor-intensive and for high rise towers inaccessible/unsafe for manual grouting
PU foam Spray costing:
Material Cost:
- One 750 ml foam can, filled (can fill up to 66 holes of 20 mm diameter * 450 mm length), Approx Cost of one 750 ml can =450 + GST.
- Per hole material cost = PU foam + Pu cleaner + Pu Gun = 6.8+.5+.5 = Rs 7.8
Labor Cost: One worker can fill approx 250 holes in a day. Per hole labor cost = Rs. 4 (Rs. 1000 per day labor cost)
- Total cost =Rs. 11.8 per hole
How can an adhesive manufacturer reduce total costs?
Total Application cost
Factors to be considered:
- cost of adhesive per unit ( ml/gms)
- quantity of adhesive per application
- labour cost for application
- Rework cost
- Warranty cost
- cost of failure
Total Application cost= adhesive cost per application+ labour cost + rework cost+ warranty cost + cost of failure
How to reduce total cost
It is imperative that an adhesive manufacturer provides inputs about reducing adhesive consumption. Few points are enumerated below:
- reduce cost per ml / gms of adhesive
- reduce adhesive usage per application- use adhesive dispensing systems
- reduce application time, labour cost- automatic adhesive application
- reduce rework, warranty, cost of failure – use right adhesive, accurate application – training users.
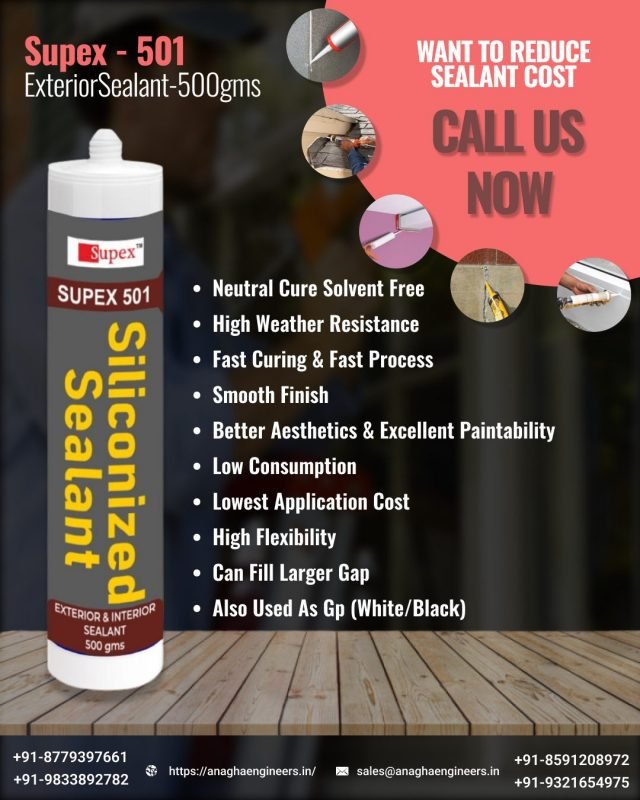
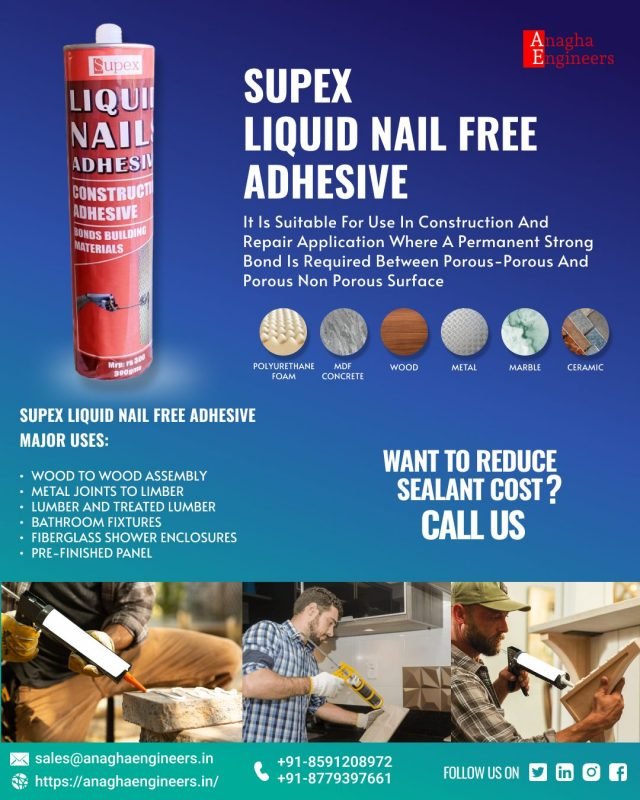
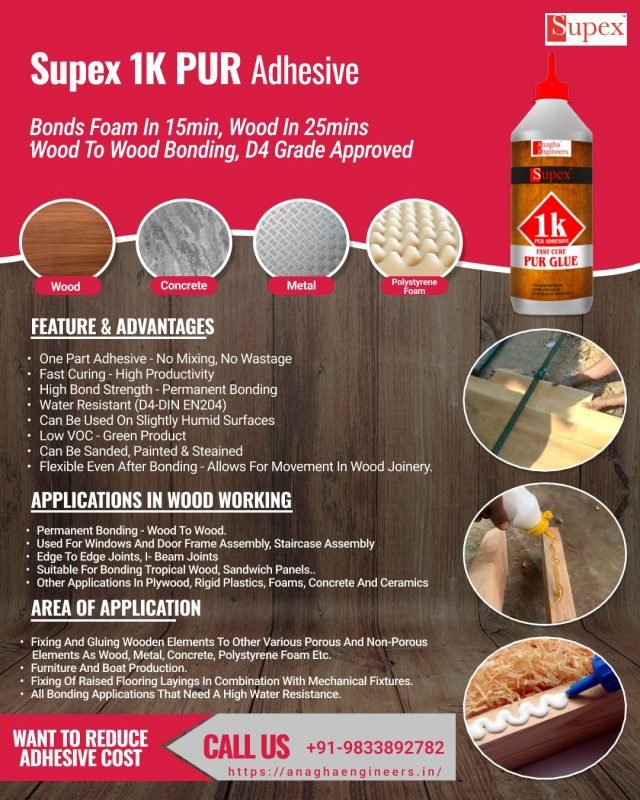

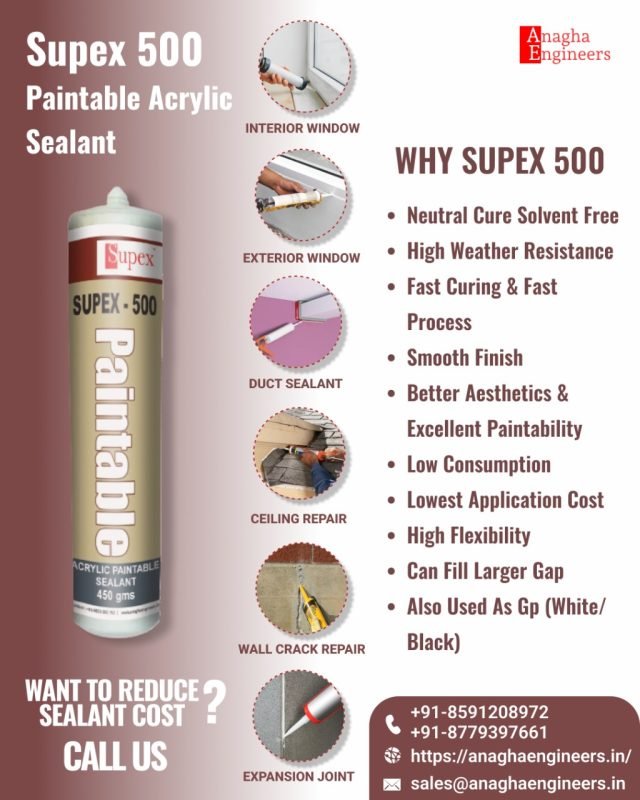
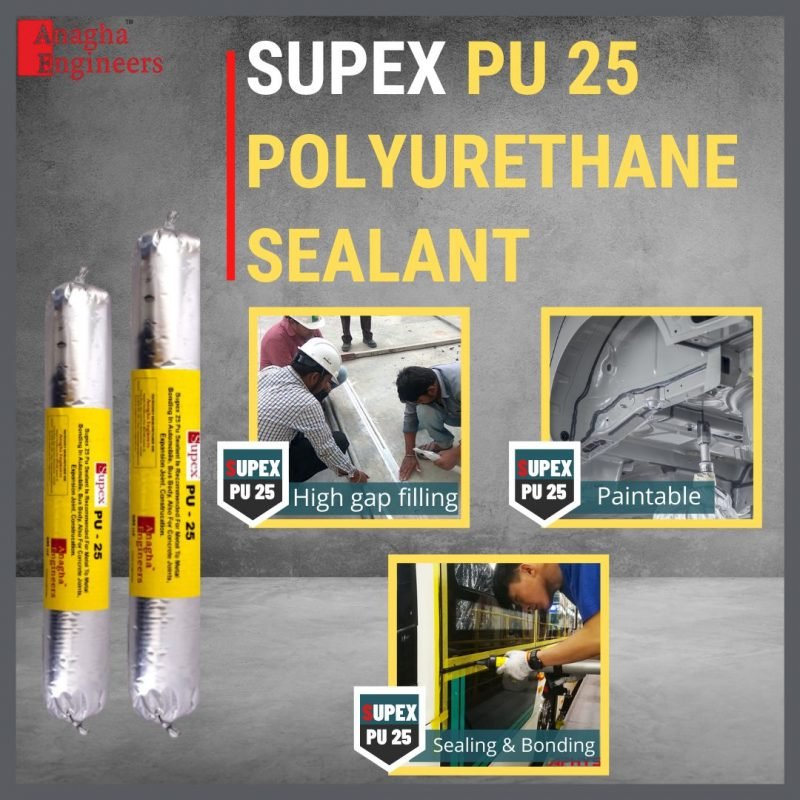
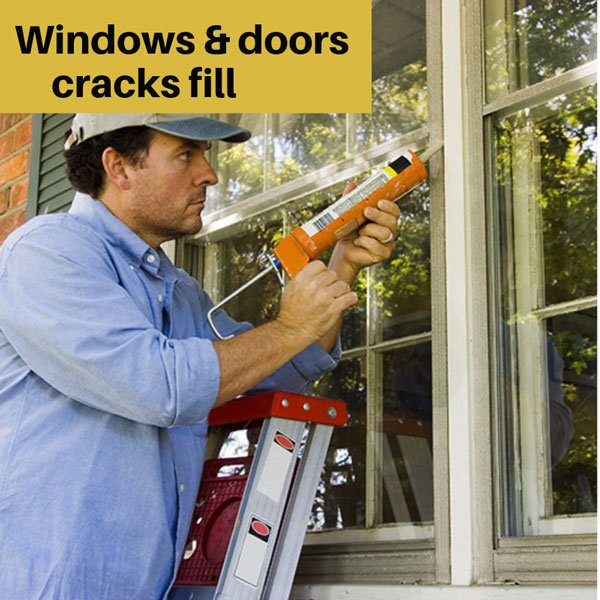
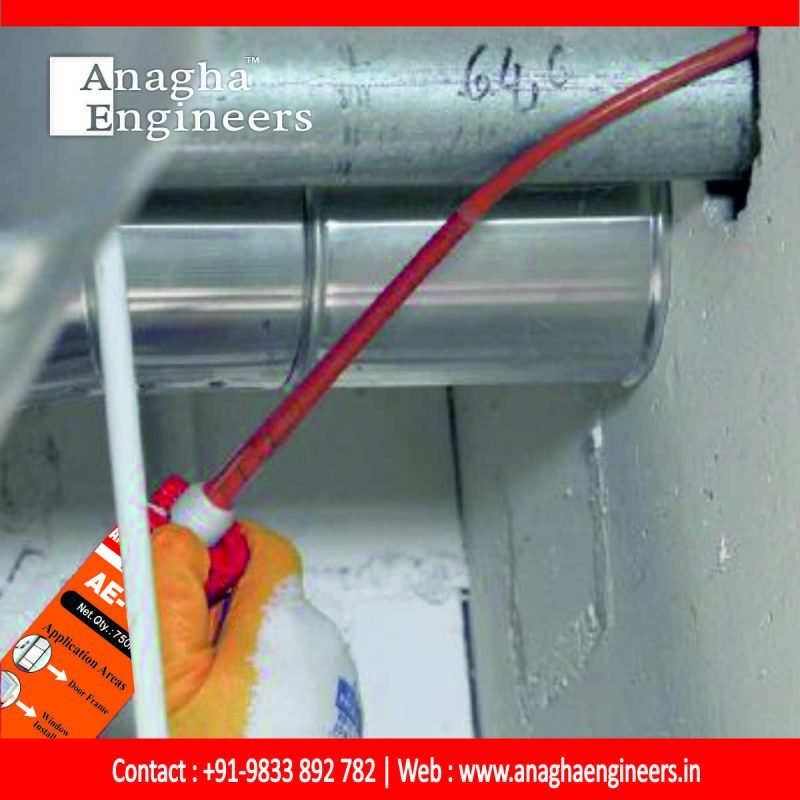
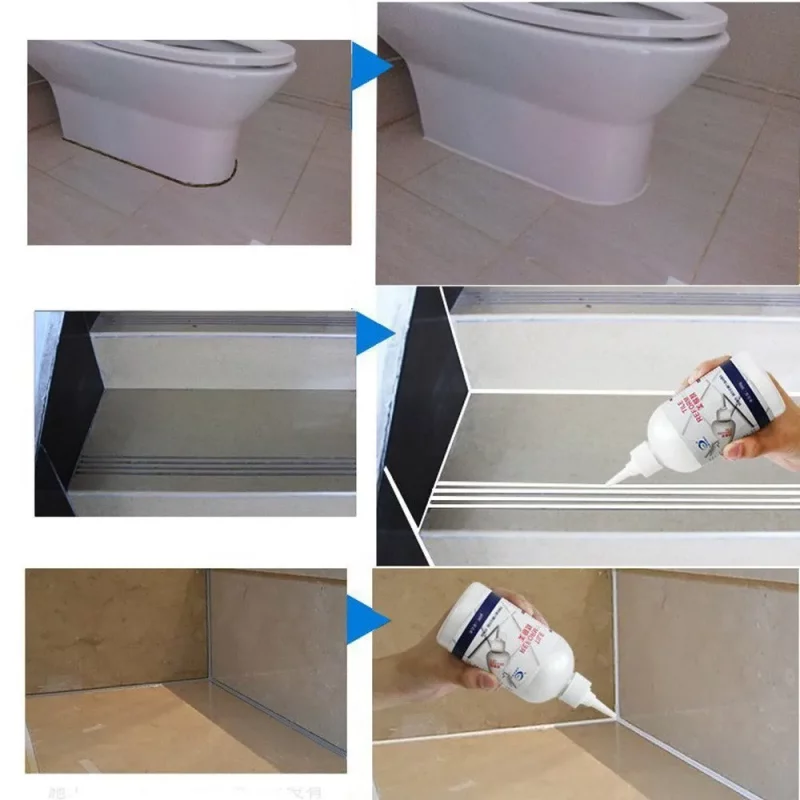
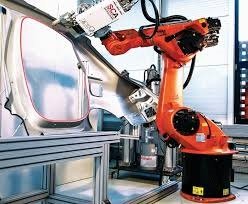
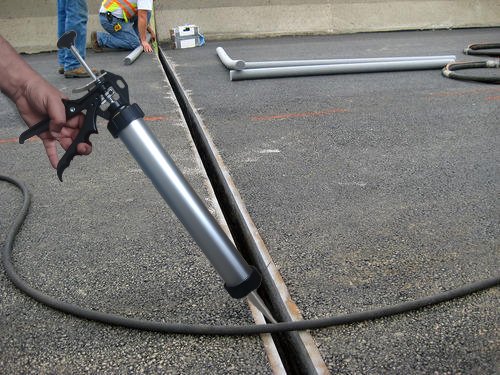
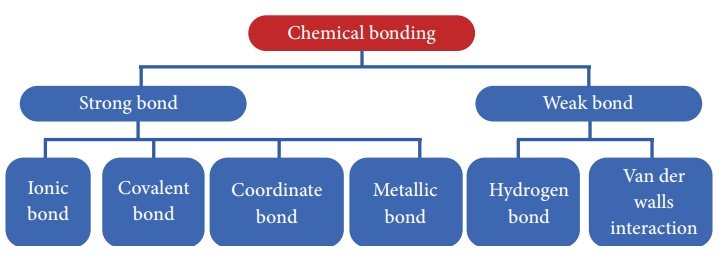
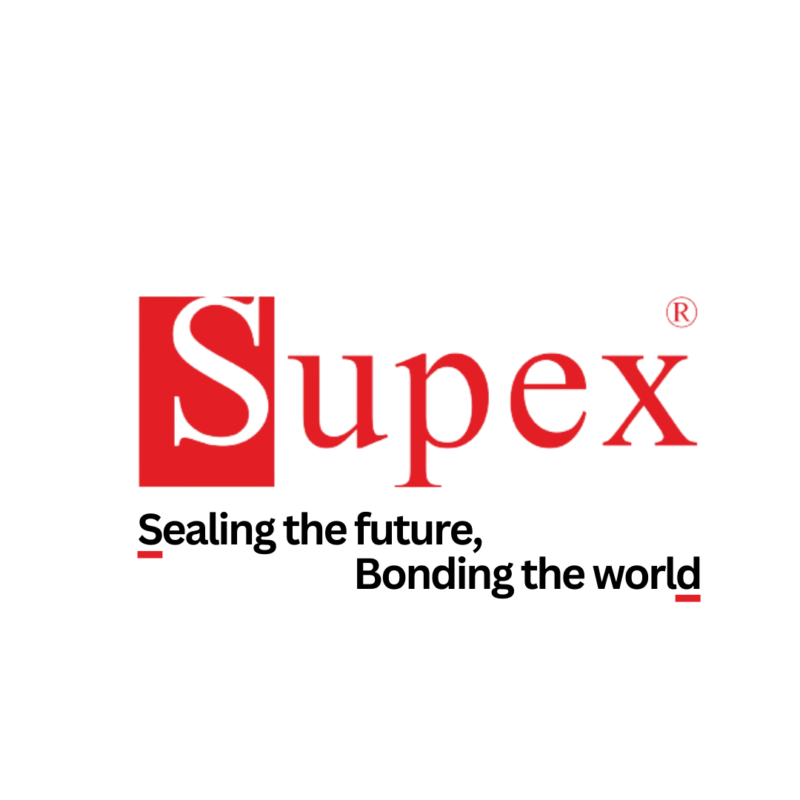