Polyurethane Adhesive for insulated panels have a big role in the quality / longevity of end use applications. Lets understand about Sandwich panels, advantages, uses etc.
What is a Sandwich Panel?
A sandwich panel is any structure made of three layers: a low-density core (PIR, mineral wool, XPS), and a thin skin-layer bonded to each side. Sandwich panels are used in applications where a combination of high structural rigidity and low weight is required.
Uses of Laminated panels
From factories to stadiums, from malls to swimming pools, sandwich panel is a durable and economic solution for many buildings. Along with industrial buildings and social areas, sandwich panel comes to the forefront as a product, preferred increasingly day by day with its new areas of implementation such as military buildings, agricultural buildings, prefabricated housing, worksite buildings, silos, and dwellings.
Composite Panel Advantages
- Fast and Easy Installation
- Perfect Thermal Insulation
- Investment Economy
- Aesthetic Appearance of Your Buildings
- High Fire Resistance
- Air and Water Tightness
- Noise-Free Buildings
Contact us for Tech support, Demo, Training
Polyurethane Adhesive for insulated panels
Call / Whatsapp: +91 9699892782, Mail: sales@supex.in
Contact us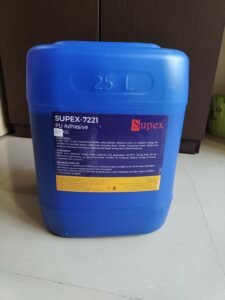
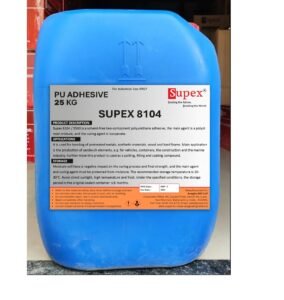
Types of Polyurethane Adhesive for insulated panels
- Two part Adhesive : 2-component solvent free adhesives consist of a resin (component A) and a hardener (component B), are mixed in a defined ratio.
Features:
- Multipurpose 2 parts PU structural adhesive
- Bonding various materials e.g. Pre-Treated Metals, Synthetic Materials, Wood and Hard Foams
- Main application for sandwich elements e.g. vehicle, container, construction industry and the filter industry
- Provide outstanding process reliability
-
One part PU: 1K PU or one-component solvent free adhesive are mainly used for panel production and thus applied on larger surfaces with medium strength requirements. They can be adjusted by varying the viscosity, density and reactivity parameters.
Features:
- Cost-effective and easy to handle
- Free of VOC
- Applicable in normal (but well-ventilated) industrial environments.
- Excellent coating thickness and machinability
- High degree of consistency
Application | Product | Type | Packing |
---|---|---|---|
GRP Composite Doors | S8605 + 6201 | 2 part | 25 kg barrel/ 200 kg drum |
GRP Composite Doors | S421A + 421B | 2 part | 25 kg barrel/ 200 kg Drum |
Sandwich Panel | S2021+ 2022 | 2 part | 25 kg barrel/ 200 kg Drum |
Solid Door Composite Door | S5906 A/ B | 2 part | 25 Kg Barrel |
Solid Door Composite Door | S5907 | 1 part | 25 Kg Barrel |
Solid Door Composite Door | S5908 | 1 part | 25 Kg Barrel |
SIP Doors. EPS/ XPS/ Rockwool | S101 | 1 Part | 25 Kg Barrel |
SIP Doors. Honeycomb | S102 | 1 Part | 25 Kg Barrel |
Cement, SBO, MGO, PUF | S2110, 2111,2112,2113 | 1 part | 25 Kg Barrel |
Supex 7221 ( A popular sandwich panel adhesive ) is a moisture curing one component polyurethane adhesive used for sandwich panel bonding. The adhesive is solvent free and, being just one-component, is easy to use in production. In the process of curing, a light foaming occurs which has a levelling effect. In the realm of safety door manufacturing, precision, durability, and reliability are paramount.
As the demand for high-quality safety doors continues to rise, manufacturers seek innovative adhesive solutions that can meet stringent requirements while streamlining production processes. Enter Supex 7221, a cutting-edge PU adhesive specifically formulated for bonding sandwich panels, honeycomb and Rockwool in safety door manufacturing.
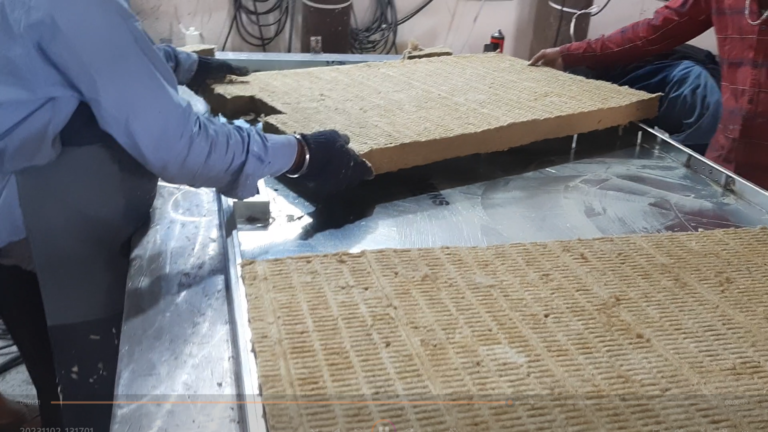
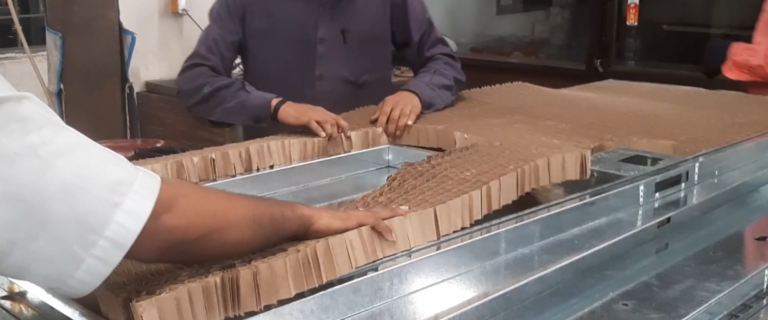
Enhancing Safety Door Manufacturing with Supex Adhesive for insulated panels
- Single-Part Adhesive: Supex 7221 is a single-part adhesive, eliminating the need for mixing and minimizing wastage. This convenience not only simplifies the bonding process but also reduces production costs associated with excess material and cleanup. Manufacturers can enjoy greater efficiency without compromising on quality.
- Fast Curing for High Productivity: Time is of the essence in safety door manufacturing. Supex 7221 offers fast curing properties, allowing for rapid assembly and increased productivity. With shorter curing times, manufacturers can optimize workflow, meet tight deadlines, and fulfill customer orders promptly, ensuring customer satisfaction and loyalty.
- Flexibility for Enhanced Performance: Safety doors are subjected to various stresses, including vibration and impact loads. Supex 7221’s flexibility enables it to withstand these challenges, ensuring durable and long-lasting bonds. Manufacturers can rely on Supex 7221 to deliver superior performance in demanding environments, enhancing the overall quality and reliability of safety doors.
- Excellent Temperature Resistance: Safety doors often undergo powder coating processes to achieve the desired finish. Supex 7221 excels in temperature resistance, ensuring bond integrity even during powder coating. Manufacturers can trust that their safety doors will maintain structural integrity throughout the coating process, resulting in a flawless finish and superior aesthetics.
- High Strength for Permanent Bonding: The strength of the bond is critical in safety door manufacturing. Supex 7221 boasts high bonding strength, ensuring permanent adhesion between sandwich panels, honeycomb, and Rockwool. This exceptional bonding capability enhances the structural integrity of safety doors, providing peace of mind to manufacturers and end-users alike.
Why Two part polyurethane adhesive for laminated board Bonding
Two-component polyurethanes ( sandwich panel adhesive) are well-known for their excellent adhesion, high mechanical properties, and good chemical resistance.
Unlike one-component polyurethane adhesives, two-component solutions are comprised of a resin and a hardener, such as polyols and poly-isocyanate polymers, that must be mixed together prior to application. While the ratios of each component may vary, proper mix ratio and complete mixing are vital to causing a chemical reaction and reaching suitable properties for a specific application. 2KPU have the advantages of single component polyurethane adhesives but are able to cure more quickly through larger gaps and are not dependent on moisture or heat to cure.
Advantages two-component polyurethane adhesive
- Strong bonding to heighten durability.
- Better chemical resistance compared to one-component polyurethane adhesive.
- Automatic dispensing capabilities and quick cure speed to improve production efficiencies.
- Ability to cure quickly and in a definite time for an application adapted to your lean manufacturing needs.
- High versatility and optimization of mechanical properties for enhanced performance.
- Multi-substrates adhesion to increase design options.
- Environmental compatibility with recyclable or partially bio-based adhesives
Supex 8104 + Hardener : 2 C PU adhesive for Laminated board bonding
Supex 8104 is a solvent-free two-component polyurethane adhesive, the main agent is a polyol mixture, and the curing agent is a polymeric MDI.
Application area:
Suitable for the bonding of refrigerated carriages, building exterior wall integrated board, honeycomb board, outdoor sunshine board and other boards
How to use 2c PU adhesive,S-8104
Before use, this product ensures that the adhesive surface is dry, free of dust and grease.
S8104 and curing agent( Hardener) are weighed in proportion and stirred evenly, and the scraper, drum, glue shower machine and other tools with serrations can be applied.
S-8104 curing time can be reduced by increasing the temperature or adding the catalyst, ensuring that the adhesive surface is tightly bonded during the curing process.
Wash:
Uncured adhesives for sandwich panel can be removed with a special cleaning agent, aftr curing it can only be removed mechanically.